Longuer life of cutter tools
Select the best tools for cutter head is one of the main challenges of all TBM Engineers.
The goal is not only reduce cost, it is also a subject of risk reduction.
The benefits of long life cutter tools are:
OUR EXPERIENCE
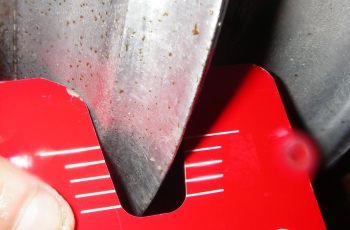
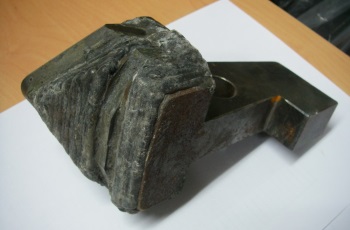
We took care of this issue in a soft ground tunnel jobsite. The tunnel was for the construction of urban rail, so the tunnel trace was under city streets, and under populated buildings too.
The Contractor had a great concern about the wear of cutterhead tools because it was not possible to stop the TBM where desired due to the settlements which it could produce. The earth pressure was around 2,5 bar, and interventions in cutterhead could only be done in hyperbaric conditions, by divers.
There were ventilation shafts and stations every 500 meters, so the goal was to advance from shaft to shaft, without intermediate stops.
A strong kind of cutterhead tools was selected for this purpose. It consisted in single piece scrappers with 4 rows of tungsten carbide. The small tools were equipped with two rows as well. Finally, all the surface in touch with the ground was covered by a thick layer of hardfacing which contained tungsten carbide small particles, surrounded by a matrix of hard metal.
This layer of hardfacing protected the tungsten carbide rows while the TBM crossed the diaphragm walls. Besides, the housing of tungsten carbide inserts was protected more time, so the teeth and scrappers were consumed in a proper way.